1 引言
國內(nèi)電機(jī)行業(yè)過去一直使用成形立銑刀加工電機(jī)轉(zhuǎn)子下線槽槽口。由于受電機(jī)轉(zhuǎn)子下線槽槽寬的限制,這種立銑刀直徑較小、有效齒數(shù)少,因此其整體剛性較差、加工效率不高。為提高加工效率,目前不少電機(jī)生產(chǎn)廠已改用盤形可轉(zhuǎn)位槽口銑刀在帶交叉銑頭的轉(zhuǎn)子銑床上進(jìn)行加工。由于這種成形盤銑刀的直徑不受電機(jī)轉(zhuǎn)子下線槽槽寬的限制,因此刀盤直徑可設(shè)計(jì)得較大,使參與加工的有效齒數(shù)增加,容屑槽增大,從而可顯著提高加工效率。但由于該銑刀的可轉(zhuǎn)位刀片之間的搭接精度要求較高,因此設(shè)計(jì)、制造難度較大。如采用傳統(tǒng)的設(shè)計(jì)、加工方法,很難達(dá)到使用要求,且效率較低。為此,我公司引進(jìn)德國英格索爾MAX-1型可轉(zhuǎn)位銑刀的設(shè)計(jì)、編程、生產(chǎn)技術(shù)以及美國SDRC公司的1-deasCAD/CAM應(yīng)用軟件,成功設(shè)計(jì)、制造出了加工電機(jī)轉(zhuǎn)子槽口的專用盤形可轉(zhuǎn)位銑刀。
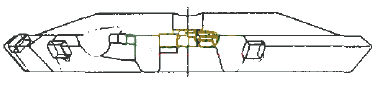
圖1 盤形可轉(zhuǎn)位抽口銑刀的結(jié)構(gòu)
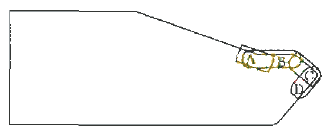
圖2 刀片搭接圖
2 盤形可轉(zhuǎn)位槽口銑刀的特點(diǎn)
盤形可轉(zhuǎn)位槽口銑刀的結(jié)構(gòu)見圖1。該刀具具有以下特點(diǎn):①采用英格索爾MAX-1型立裝刀片結(jié)構(gòu),刀具在切削過程中主要靠切削力夾緊,只需用一個(gè)螺釘對(duì)刀片定位、緊固,因此結(jié)構(gòu)簡(jiǎn)單可靠,刀片更換方便,定位準(zhǔn)確;②刀具采用切向定位安裝方式,可承受較大切向力,刀片不易磨損和崩刃,且磨損區(qū)域較寬;③刀盤直徑和容屑槽較大,可采用大進(jìn)給量、大切深進(jìn)行切削;④為減小銑削時(shí)的最大切削力及切削力波動(dòng),刀片采用不等分排列,使各刀片承受的切削載荷基本均勻。因此,使用該刀具加工電機(jī)轉(zhuǎn)子下線槽槽口可大大提高加工效率。
3 盤形可轉(zhuǎn)位槽口銑刀的設(shè)計(jì)
銑刀設(shè)計(jì)內(nèi)容包括:①采用CAD技術(shù)在計(jì)算機(jī)上繪制電機(jī)轉(zhuǎn)子下線槽槽口的標(biāo)準(zhǔn)型線;②對(duì)型線進(jìn)行分段,并用相應(yīng)硬質(zhì)合金刀片的刀刃組成各段型線;③根據(jù)刀具型線設(shè)計(jì)刀片形狀,并將設(shè)計(jì)好的刀片擺放到下線槽槽口的標(biāo)準(zhǔn)型線上,形成如圖2所示的刀片搭接圖。
電機(jī)轉(zhuǎn)子下線槽槽口的標(biāo)準(zhǔn)型線由A、B、C、D四個(gè)刀片搭接而成。刀片按槽口標(biāo)準(zhǔn)型線搭接完成后,刀片在刀體上的最終位置通常采用直接轉(zhuǎn)后角法或刀片錯(cuò)位法確定。直接轉(zhuǎn)后角法是將刀片排列好后,直接繞刀片的切削刃轉(zhuǎn)一個(gè)后角。該方法型線準(zhǔn)確,但在刀盤圓周上不能形成側(cè)隙角,因此切削時(shí)會(huì)發(fā)生干涉,難以滿足該刀具的使用要求。刀片錯(cuò)位法是利用刀片錯(cuò)位形成后角落差,同時(shí)在圓周上可產(chǎn)生側(cè)隙角。該方法的缺點(diǎn)是切削刃存在一定的直線度誤差,但計(jì)算表明,該誤差只有千分之幾毫米,遠(yuǎn)小于下線槽槽口的精度要求,因此該方法適用于該銑刀的設(shè)計(jì)。具體設(shè)計(jì)步驟如下:
計(jì)算刀片錯(cuò)位值Y 按照英格索爾MAX-1型可轉(zhuǎn)位銑刀的結(jié)構(gòu),將刀片進(jìn)行錯(cuò)位,形成落差。計(jì)算刀片錯(cuò)位值Y的經(jīng)驗(yàn)公式為
當(dāng)N=(R2-H2)½時(shí):Y=H
當(dāng)N≠(R2-H2)½時(shí)::Y=(H2-N2+2NR)/(2H)式中:R——刀具半徑
H——刀片厚度
N——后角落差
刀片錯(cuò)位
計(jì)算出每個(gè)刀片的錯(cuò)位值Y后,選取刀片上一點(diǎn)作為基準(zhǔn)點(diǎn),測(cè)出其半徑R,然后將刀片錯(cuò)位Y值后再橫移x值(x=(R2-Y2)½),刀片即可形成后角及圓周側(cè)隙角。
刀片角度修正
由于刀片錯(cuò)位使切削刃發(fā)生了變化,因此必須對(duì)刀片在型線上的角度加以修正。首先在計(jì)算機(jī)上測(cè)出刀片切削刃兩端點(diǎn)的半徑值R及軸向差值dx,計(jì)算出實(shí)際切削刃與軸線的夾角(=arctan(R1-R2)/d2);然后將理論值相減,求出修正值;將刀片旋轉(zhuǎn)角后再測(cè)量一次實(shí)際夾角,如誤差大于0.01°(相當(dāng)于2µm的直線誤差),則需再次進(jìn)行修正,直至刀片的實(shí)際偏角與標(biāo)準(zhǔn)型線相吻合,滿足規(guī)定要求為止。
其它尺寸設(shè)計(jì)
完成一組刀片的錯(cuò)位修正后,根據(jù)刀片位置設(shè)計(jì)出刀片的容屑槽、空刀孔、螺釘孔等尺寸。
確定刀片組數(shù)
根據(jù)刀體尺寸確定該銑刀的刀片組數(shù)。由于圓周齒的切削量較大,因此每組刀片應(yīng)多增加一片圓周齒刀片。
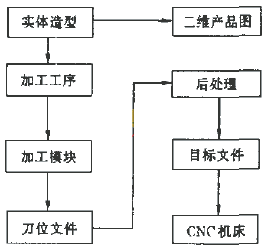
圖3 刀具的設(shè)計(jì)加工流程
4 盤形可轉(zhuǎn)位槽口銑刀加工程序的設(shè)計(jì)
在完成盤形可轉(zhuǎn)位槽口銑刀刀體的CAD設(shè)計(jì)后,即可利用CAM模塊對(duì)刀體進(jìn)行仿真加工。刀具的設(shè)計(jì)加工流程如圖3所示。
設(shè)計(jì)加工工序?yàn)闇p小重復(fù)定位誤差,該銑刀采用一次裝夾完成全部加工過程。刀片槽的加工共設(shè)計(jì)了8道工序:銑空刀→銑容屑槽→粗銑刀片槽→半精銑刀片槽→螺釘孔定中心→鉆螺紋底孔→攻絲→精銑刀片槽。根據(jù)設(shè)計(jì)的工序,加工系統(tǒng)能自動(dòng)選擇相應(yīng)的刀具及合理的切削用量和加工余量。
生成加工程序
加工工序設(shè)計(jì)完成后,加工模塊根據(jù)需要加工的內(nèi)容安排加工路線,并按設(shè)計(jì)的工序進(jìn)行仿真加工;確定加工工序正確無誤后,即可生成加工該刀具的刀位文件;然后選擇所用機(jī)床的后處理程序?qū)Φ段晃募M(jìn)行后處理,生成機(jī)床加工用的目標(biāo)文件(G代碼文件);最后還需對(duì)該文件進(jìn)行編輯,去掉仿真過程中一些不必要的語句,生成最終的加工程序。
試加工與檢測(cè)
將最終生成的加工程序傳輸?shù)较鄳?yīng)的加工中心上,對(duì)工件進(jìn)行試加工,并在投影儀上對(duì)加工出來的一組刀片進(jìn)行檢測(cè)。如刀片搭接型線與標(biāo)準(zhǔn)型線放大圖一致,說明加工程序正確,即可按此進(jìn)行生產(chǎn)性加工。如加工出的刀片不合格,則需分析查找問題。如是仿真加工的問題,還需進(jìn)行以M修正,直至加工出合格成品。